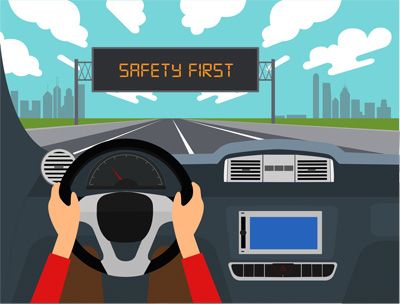
What Utility Fleets Can Do to Improve Driver Safety Performance
- Containing Contagions in Close Quarters
- What Utility Fleets Can Do to Improve Driver Safety Performance
- An Electric Pickup to Watch: The 2022 Rivian R1T
- Using Telematics to Drive Fleet Safety Improvements
- 14-Point Checklist for Spec’ing Impact Attenuators
- Power Ahead: The Coming of Hydrogen Fuel-Cell Trucks
- Winterizing Your Crews
- Stocking Critical Parts in a Supply Chain Crisis
- Win Them Over
How much does a vehicle collision cost your company in property damage, health care expenses, lost worker days, legal fees, and other direct and indirect costs?
According to the latest report by the Network of Employers for Traffic Safety, available at https://trafficsafety.org, U.S. employers across various industries paid:
- $26,081 per crash in property damage.
- $78,418 per injury.
- $751,382 per fatality.
These numbers may or may not reflect your company’s data. But they do provide a useful frame of reference to drive home the fact that a strong commitment to driver safety protects not only drivers but also your company’s reputation and bottom line.
After all, when a truck displaying a utility’s logo hits another vehicle or a pedestrian, it becomes a prime target for media attention and legal action.
But as a fleet manager, what can you do to help prevent crashes? In many cases, you’re not responsible for screening, hiring, training or coaching company drivers. Yet your department must deal with a significant piece of the fallout from each incident as you and your team scramble to find suitable replacements for vehicles that are unexpectedly – and often permanently – taken out of service.
So, what can the fleet department do to help move the needle on improving driver safety and reducing collisions? Try these three strategies.
1. Spec for safety.
Debbie Daniel, manager of consulting analytics at Donlen (www.donlen.com), a fleet management company, started seeing a new trend in fleet purchasing strategies a few years ago.
“Historically, when it came to selecting vehicles, fleets would focus on the total cost of ownership: What’s the most optimal vehicle choice in terms of acquisition, remarketing, fuel and maintenance costs? But in the past three or so years, the availability of safety options has emerged to become a big player in vehicle decisions as well,” Daniel said.
Why the shift?
Until recently, factory-installed advanced driver assistance systems (ADAS) – such as automatic braking, parking assist, blind-spot detection, rear cross-traffic alerts and lane-keeping assist – were only available in the more expensive trim levels for most vehicle segments.
“Customers didn’t want to go up to the highest trim level to get those safety features that drive up the cost significantly,” Daniel said. “They wanted to get those features in the base models but couldn’t. But that started to change right around 2018.”
Today, GM, Ford and RAM now offer ADAS options in their base model light-duty pickup trucks for a premium of about $1,200 to $2,000 – a more feasible price tag for fleet managers to build a business case around.
“If you have the data, you can work with the safety department to say, ‘Here’s the number of front-end crashes, backing collisions and incidents from changing lanes we’ve had.’ And then discuss how the new safety systems can help reduce those collisions – and the costs associated with them,” said John Adkisson, a fleet industry veteran who has worked for PPL Electric Utilities and Asplundh Tree Expert LLC.
“It’s an easy sell to say, ‘Sure. It’s going to cost an extra $2,000 a unit. But we’re doing this to improve driver safety.’ And then you evaluate over the next year or so to see how the safety record of the new trucks compares to that of the other vehicles.”
2. Translate the data.
Telematics is a powerful tool to monitor and detect unsafe driver behaviors, such as rapid acceleration, hard braking and speeding.
But having the ability to capture driver data is not enough. You must also be able to translate what that information means to the operations groups and how they can use it to improve the organization’s overall driver safety performance.
“As the fleet manager, your job is to decipher what all that [telematics] data means to the operations groups,” Adkisson said. “This way, they can trust the data and determine whether or how they should act on it or not. After all, as a fleet manager, I don’t have control over the drivers. But if I have access to the data, I must provide it in a way that minimizes the pain for the operations groups to get the information and help them decipher what to do with it.”
3. Facilitate quicker reporting.
The daily vehicle inspection process is a crucial component of any driver safety program because it’s intended to uncover potential issues on vehicles before they lead to catastrophic component failures that put the operators – and the public – at greater risk on the roads.
If a driver documents a potential problem during a daily inspection, they need a way to communicate that issue with the fleet department to get it remedied quickly.
And that’s an area you can influence as a fleet manager to impact driver safety significantly.
“Technology is getting to the point where the fleet manager can facilitate the daily maintenance by ensuring that the driver is engaged in the process to look for certain things and report any issues as soon as possible,” Adkisson said. “It could be through an app or some other electronic means to document any issues and provide a speedy way to get that information to the fleet department to schedule service to fix it. The driver can use a phone app that takes pictures of the problem and scans a barcode – something that’s easily put onto the vehicle that has all the important vehicle information.”
The Bottom Line
If you want to help improve driver safety performance – and reduce the costs related to vehicular collisions – commit to consistent communication and collaboration with all stakeholders.
Work closely with the safety department and operations groups to develop vehicle specs with maximum safety in mind.
Communicate to the operations groups how they can use and interpret telematics data to identify reckless driving behaviors to develop strategies to mitigate those risks.
And look for ways to use technology to make it faster and easier for drivers to communicate any vehicle issues to your department – to prevent potentially dangerous breakdowns on the road that could put those drivers’ lives at risk.