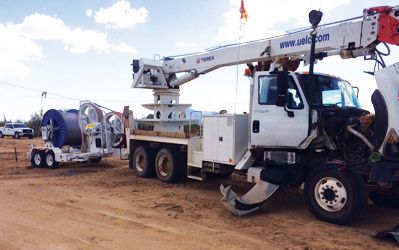
Protecting the Fleet Mechanic
A number of years ago, I went to a construction job site to participate in the morning crew meeting tailboard. The construction project was a 90-mile double-circuit transmission pull. The new circuit was being constructed in an existing transmission line right-of-way that had two existing energized 345-kV circuits running parallel to the new circuit construction. The location where we met was a pulling site. Crews had already been pulling at the location for two days. The work that had been completed the day before left conductors pulled in about halfway. Both ends had been caught off with chain hoists overnight so that the conductor was still under tension on the tensioner near the location of our meeting. The conductors at the tensioner had been temporarily grounded to a driven ground rod for the protection of the lineworkers. Red barricade tape also was completely encircling the tensioner, the reel trailer and the 30-ton crane hooked to the reel trailer.
I was standing near the back of the assembled group of about 20 personnel, listening to the site superintendent who was conducting the safety topic on grounding for protection from induced voltages. While he spoke, I noticed movement some 100 yards past him at the front of the 30-ton crane that was anchoring the reel trailer and tensioner. It was a fleet mechanic. He was working on an oil leak, which is one of the things mechanics do. The problem was that while the mechanic was conducting that repair task, he was in a position that exposed him to electrocution. The mechanic was there working with the full knowledge of the superintendent who was delivering the safety talk. But while the superintendent spoke to the crews about isolation, grounding and the hazards of induction, the mechanic was doing exactly what the site superintendent was telling the line crews not to do.
I have witnessed this situation on a number of occasions: Workers on a job site have a good handle on their hazards and hazard control but completely miss the risks to the lone mechanic working in the background. The act isn’t intentional. We might call it tunnel vision. The crew is focused on the wire, the tension, the rigging and the procedures associated with construction of a power line. The mechanic is practically unnoticed in the background, servicing trucks, making minor repairs and checking stickers. Sometimes it seems the only time we notice the mechanic is when he wants to take away one of our trucks. But it’s not unheard of for mechanics to get hurt on job sites. It is rare, but that’s because of the numbers. A utility or contractor may have 300 employees and six mechanics in the field. There may be 150 trucks in the field, but with six mechanics, only a few trucks at a time are being worked on at the job site. The risk occurs when a truck is exposed to an electrical hazard. If the mechanic is not familiar with the nature of the hazard, he is at risk.
The Right Circumstances
In the opening scenario, the truck that the mechanic was working on was hitched and chained to the tensioner. The tensioner was rigged to 2.5 miles of 1590 aluminum conductor strung on isolated travelers between two energized 345-kV circuits. That stringing scenario is an extreme induction hazard risk for any equipment in contact with the conductors. In this case, the mechanic had no idea what induction was or how the Freightliner tractor he was working on could have electrocuted him under the right circumstances.
Let’s spend a minute attempting to understand what is meant by “the right circumstances” as well as talking about the hazards associated with induction. There are two ways for a truck to become energized. One is pretty obvious: The operator sticks an aerial boom into the energized circuit, or the crew loses control of a conductor and it falls on the truck. Those are the most common scenarios but by no means the only ones. In those cases, there is little risk to the mechanic because it is rare that he would be working on a truck while it is engaged in hot work. A more subtle risk is presented by the risk of induction. With induction, a truck does not have to be close to energized lines to become a risk. A very simple explanation is that induction is created by the invisible magnetic field that exists around an energized conductor. The higher the voltage, the stronger the magnetic field. If a crew strings a conductor through the magnetic field, voltage will appear on the conductor plus anything in contact with the wire, such as a tensioner and truck. This magnetic field is AC electricity, and lineworkers are killed by it every year.
Generally, crews install grounds to collapse the measurable voltage created by induction. Grounding puts the voltage on the conductor at ground potential, meaning the voltage between the wire and earth is zero. However, grounding may create a false sense of protection for the mechanic who is not trained to understand the hazard of induction. Grounding can eliminate or collapse the voltage to zero, but that does not eliminate the current flowing in the pathway through the conductors and across the tensioner and truck. Under the right conditions, a mechanic in contact with a truck energized through induction can be electrocuted by that flowing current.
Induction is not the only subtle electrical hazard associated with trucks. Most mechanics are familiar with grounding of trucks, but few of them are properly trained to understand what grounding does and – even more importantly – what hazards are created by grounding trucks. Consider this: How many companies would allow a fleet mechanic to get in a bucket truck and boom himself up to the system neutral to make barehand contact with the conductor? Hopefully not even one. The system neutral is a current-carrying conductor that, in several scenarios, can have a high enough voltage on it to result in a severe injury or death. But few companies even think about the mechanic working on a truck that is grounded to a pole bond or system neutral. What’s the difference? There is no difference. The mechanic touching a grounded truck is at the same risk as if he had gone up the pole and made contact with the neutral, yet few companies recognize this risk, much less train their mechanics to recognize it.
There is one additional common risk – ground gradients – that we need to cover before we address the solution to this problem. You may recall that in the narrative at the beginning of this article, the tensioner, trailer and truck were encircled by red barricade tape. The red barricade tape denoted a boundary for a no-entry space around the equipment. The space was designed to protect workers from voltage that can appear in the earth around a truck when the truck is exposed to an electrical charge like induction. If the truck becomes energized, the ground around the truck becomes energized. Anyone in that space is at risk of electrical injury.
There is no particular rule about how far away from a truck the barricade tape should be placed. That determination is made by qualified persons who understand the dynamics of the exposure created by the work environment. The barricade tape itself, whether it is red or yellow, has no protective value. It only serves to protect workers if workers understand the meaning of the barricade, its purpose and its limitations. In the opening scenario, the mechanic was inside the barricade tape working on a truck that was subject to energizing by induction. The mechanic had no idea about gradients or the hazard they represented. He thought the barricade was for when the crew was actively pulling wire, to protect people from failed rigging and line-of-fire hazards.
The Solution
The solution to this problem is found in what I have come to call “the continuum of safety.” The word “continuum” simply means a continuous interconnected process. In a continuum, the groups in a process are not perceptibly different from each other, but the extremes within the groups are distinct. Whether you are a contractor or utility, every group has its own sandbox where you have certain procedures, responsibilities, processes and goals. Departments evolve. Without intending to, they become entities unto themselves. It’s not uncommon in any company to hear someone say, “That’s fleet’s job” or “That’s engineering’s problem” or “That’s a management issue; we’re just here to fix stuff that breaks.” We isolate responsibilities without even thinking about it. There is a big difference between what a wire-stringing crew does and what fleet mechanics do when servicing trucks on-site, even though everyone is working toward the same goal in the same environment. The continuum of safety solves that problem, but it doesn’t happen by chance. Someone must create the process, and each of the stakeholders must understand the hazards relative to their workforce and take ownership of the solution.
In creating the process, the workplace must be audited to identify the relative hazards, resulting overlaps and related exposures that occur between the working groups. From there, the working groups must commit themselves to the training necessary to assure that workers in the groups understand those identified exposures.
In my experience, there is a lot of awareness training needed by fleet mechanics that doesn’t get done until someone gets hurt. Most of the time it’s that the exposure simply wasn’t recognized. We don’t need to have mechanics attend apprentice classes, but they do need to participate in awareness-level classes. Facilitators of these types of classes review the basics necessary for trainees to recognize the elements of a risk, the nature of exposure and what they must do to protect themselves. When a fleet mechanic pulls up to a job site, he should have a basic understanding of the work and be able to recognize what is being done and where the risks are. In that way, when he contacts the supervising personnel and reviews the tailboard, he is fully aware of the issues and risks and what he must do to protect himself. In the same way, crew members receive training to make them aware of the issues so that they can help to keep those working mechanics out of harm’s way when work is in progress or when procedures or tasks are changing.
If you are reading this article and need some tips or help putting a program in place to protect your field mechanics, please contact us. We will point you in the right direction.
About the Author: After 25 years as a transmission-distribution lineman and foreman, Jim Vaughn, CUSP, has devoted the last 20 years to safety and training. A noted author, trainer and lecturer, he is a senior consultant for the Institute for Safety in Powerline Construction. He can be reached at jim@ispconline.com.