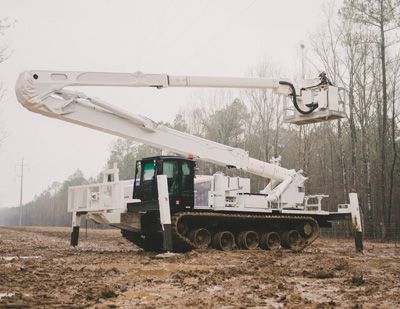
Avoiding Costly Mistakes with ATUVs
Prices can range upward of $300,000 for a ready-to-work all-terrain utility vehicle (ATUV), so fleet managers can ill afford missteps in spec’ing, maintenance or planning – mistakes that may end up costing unnecessary dollars or lost days on a remote site while waiting for repairs.
Fortunately, mistakes can be avoided with smart spec’ing and common-sense practices, according to ATUV chassis manufacturers.
Right-size spec’ing is the most important thing fleets can do, said Matt Slater, vice president of sales and marketing with Terramac (www.terramac.com).
“[Make] sure you are sourcing the right size unit for your application,” he said. “Problems [can] arise when you source too large an attachment to go on a unit or try to use a smaller unit to make it easier to transport. The inability to move [equipment] on a specific trailer or to get permits for it is something we see all the time.”
Ignoring maintenance practices and/or recommended procedures also can cost fleets big dollars, especially if those processes end up voiding the warranty. Overloading a unit beyond the rated carrying capacity and failing to perform recommended service are two examples of warranty-voiding actions, Slater said. Another is adding unapproved attachments, such as a lift that is too high for the carrier’s footprint.
“This is why we work closely with customers to ensure the carrier and attachment are a proper fit for each other,” Slater said.
The good news, ATUV manufacturers said, is that mis-spec’ing new equipment is becoming more difficult because they work hand-in-glove with equipment suppliers to make sure the units are matched correctly to the customer’s order.
Issues are more likely to occur with a fleet mounting older equipment onto a new chassis, said Alain Chabot, product manager with PRINOTH Tracked Vehicles (www.prinoth.com). “Through our knowledge of technology and together with our engineering team, we can support our customers to fully integrate the implement onto the crawler carrier. We can’t expect every customer to be a specialist on our product, and that’s why we offer this kind of additional support and collaborate to mount the equipment the same way they would on a truck,” he said.
“When we redesigned our PANTHER chassis, including the T16 chassis, we wanted to facilitate implement installation for customers, which we achieved with a standard C-channel truck-style chassis,” Chabot added. The outcome is that installing a crane on PRINOTH’s crawler carrier doesn’t take much more time than on a regular truck. “This is a huge benefit for equipment suppliers and helps reduce potential mistakes,” he said.
Because ATUVs are so specialized, and because they can cost so much, most buyers are experienced with the unit’s capabilities, tend to know what they need and, as a result, don’t make many mistakes, said Curt Unger, sales manager with Morooka USA (www.morookacarriers.com).
“It’s really hard to wear these little machines out, and it’s true, they can generally hold more than they’re rated for,” Unger said, referencing Morooka’s line of compact carriers. “But a sure way to shorten the useful life of their components, especially their undercarriages, is to repeatedly overload them.”
That can be especially costly for rental customers, he added. “Damage of any kind to the unit, including damage to the undercarriage, can add extra charges to [a fleet’s] rental bill,” Unger said.
Beyond that is the issue of what overloading does to operating performance. “To wear something out, you might have to repeatedly overload it,” Unger said. “But it only takes one incident to have a mishap. Each time you load your machine beyond its rated capacity, what have you done to its center of gravity? How have you compromised its safety on a slope?”
While the manufacturers contend they have essentially reduced the chance for mistakes by better engineering, stuff happens. Spec’ing smartly and operating within the ATUV’s rated parameters sounds like the best advice to avoid costly mistakes.
About the Author: Jim Galligan has extensive experience covering the commercial truck transportation and utility fleet sectors.
*****
From Wheels to Tracks: Three Tips for Smart Spec’ing
All-terrain utility vehicle manufacturers contend that the close relationships they have with equipment suppliers have gone a long way in helping fleets avoid costly spec’ing mistakes with their ATUVs.
One exception may be with customers who aren’t familiar with the differences in wheeled versus tracked equipment as they change from the former to the latter, said Curt Unger, sales manager for Morooka USA.
In those situations, Unger recommended that fleets consider three factors: speed, size requirements and operator training.
The first mistake a fleet might make is underestimating the need to transport material quickly, Unger said. Put simply, wheeled vehicles are faster than tracked units. “If your tracked vehicle’s top speed is 8 mph, and it’s a 4-mile drive one way to the site, you’re going to lose an hour for every roundtrip you make,” Unger noted. “Wheeled vehicles have the advantage of speed on ground conditions that permit their use.”
Next is properly sizing the equipment, not just for capacity but also for its weight and dimensions. Tracked vehicles can weigh more than a wheeled counterpart, and fleets need to take that into consideration, Unger said. The Morooka MST600, for example, weighs almost 10,000 pounds empty. “You will no longer be able to carry this and your mini-excavator to a job site behind your pickup on a 12,000-pound trailer,” he said.
Finally, don’t underestimate training requirements. Some ATUVs have a steeper learning curve, as does the transition from wheeled utility vehicles to tracked machines. “A tracked machine will feel as though it will climb up a vertical wall, but there’s a limit to how much slope you’ll be comfortable traveling on horizontally,” Unger said. “Operators need training about the limitations of the rig and traveling different kinds of surfaces.”