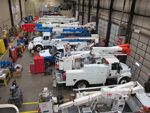
Green Shops
Nicor Gas
Nicor Gas, headquartered in Naperville, Ill., is one of the nation’s largest gas distribution companies. Owned by Nicor Inc., a holding company, Nicor Gas serves 2 million customers in a service territory that encompasses most of the northern third of Illinois, excluding Chicago.
“We look at environmental compliance as an opportunity for continuous improvement,” said Jeff Price, manager, fleet operations at Nicor Gas. “We are always seeking out best practices and applying them whenever feasible. For example, as shop equipment becomes dated, we look at the environmental benefits as well as the functionality of replacement technologies.”
Servicing approximately 2,000 units, Nicor’s fleet management department operates five large maintenance facilities and seven satellite shops throughout northern Illinois. The department has a total staff of 57, including 47 hourly employees who are directly involved in maintenance operations, and eight management personnel.
Price related that Nicor Gas has constructed a new maintenance facility that opened in December 2009 and that the utility is building another new shop that was scheduled for completion by the end of 2011. “In these locations,” he said, “we have several environmentally friendly features, and our goal is to have the structures certified as energy efficient. To achieve that, among other things, we have included prism sunroofs, high-efficiency fluorescent lighting, radiant floor heating and variable speed exhaust systems in the design. We are also moving away from chemical solvent tanks to hot water alternatives, and we’re using recycled glycol products, and are considering a similar program for our base engine oil products to the extent one is available.
“When it comes to ensuring compliance with environmental regulations,” Price continued, “our environmental, health and safety department does an excellent job inspecting our sites. We also stay abreast of changes through our alliances with vendors, associations and best practice seminars. If a change is identified, we take steps to handle these in a timely, efficient and economical manner.”
One way that Nicor Gas is meeting the challenge of addressing changes in and ensuring compliance with environmental regulations is through annual compliance training, monthly formal updates and refreshers in the form of tailgate meetings. “We take the training of our employees seriously and will continue to do so,” Price stated. “Occasionally, we look to outside sources to keep our techniques fresh and up to date.”
Price goes on to say that there is no single challenge when it comes to environmental compliance and initiatives in shop operations. “It’s more like managing the changing landscape and seeing that best practices are followed correctly,” he concluded. “We also try to follow the examples set in our communities. Many of our shop locations are in forward-thinking areas, and we want to be a good partner to these municipalities. It is our neighborhood, too, and it is the right thing to do.”
Central Hudson Gas & Electric
Central Hudson Gas & Electric Corporation, a regulated transmission and distribution utility headquartered in Poughkeepsie, N.Y., serves approximately 376,000 residential and business customer locations in eight counties of New York’s Mid-Hudson River Valley. Its 2,600-square-mile electricity and natural gas service territory extends from the suburbs of metropolitan New York City north to the state capital in Albany.
“We are constantly working to be sure we are complying with all environmental regulations,” said John McCormack, transportation foreman at Central Hudson Gas & Electric. “At the forefront of that effort is the annual hazcom training for our maintenance staff and instructional training for new employees on the use of equipment designed to help us protect the environment.”
The environmental compliance training that McCormack describes is now taking place at Central Hudson Gas & Electric’s six repair facilities. Included in the fleet’s maintenance operation is one main truck garage where all major inspections and repairs on trucks, buckets, diggers, backhoes and tractors are performed. There are also five district garages for major work and maintenance on light-duty vehicles. All of the facilities handle repairs on vehicles that are driven in and make road calls for breakdowns.
“We’re especially focused on managing the waste stream at our facilities,” McCormack stated. “Our shops no longer have any floor drains to allow anything to go into a storm drain. In addition, we’re making sure that engine and hydraulic oils, antifreeze, and used filters and tires are all being disposed of properly. We use only qualified contractors to handle that removal, and all of our vendors are registered and comply with all environmental regulations.”
Central Hudson Gas & Electric’s shops are equipped to properly and safely handle waste materials. In the truck garage there is a 500-gallon waste tank with an evacuation system to empty portable oil drain buggies and pans. The tank has an automatic alarm and shutoff to alert the staff when it is nearly full, and it will not accept oil when it is full. In the district garages there are 275-gallon waste oil tanks, which are now being converted to double wall models, and 55-gallon barrels for used filters and antifreeze.
“There are clearly benefits to all of our environmental compliance initiatives,” McCormack concluded. “A safer environment is better for our company, our employees and the communities we serve.”
Editor’s Note: Case studies on these pages have been supplied by FleetAnswers, a membership-driven Intelligent Fleet Community that connects fleet managers with industry peers, and provides tools to help improve operations, industry-specific benchmark data, and information on current trends and issues. For more case studies and other resources, visit www.fleetanswers.com.
Diagnostics Information
Mitchell 1, a Snap-on company, and Noregon Systems, a vehicle communications solutions supplier, announced an agreement to develop an interface between Mitchell 1’s Repair-Connect.net and Noregon’s JPRO Commercial Fleet Products. The new interface will enable Noregon to capture and pass a vehicle identification number (VIN) and diagnostic trouble code (DTC) into Mitchell 1’s Repair-Connect.net application. According to the companies, instantaneously delivering DTC-specific diagnostic and repair information to service personnel will shorten the time between an initial diagnosis and a completed repair, reducing downtime for service.
Mitchell 1’s Repair-Connect.net Web-based application uses DTCs to gather information required to fix a problem. Seven tabs presented in the Repair-Connect program contain details specific to the reported DTC, such as component location, connector views, removal and installation, wiring diagrams and specifications. The new interface will enable Noregon to capture and pass a VIN and DTC into Mitchell 1’s Repair-Connect.net and retrieve related service information, including a description of the trouble code, wiring diagrams, component connector views, electrical component locations, testing, removal and installation procedures, and specifications.
Noregon’s JPRO Commercial Fleet Products are PC- and adapter-based in-shop diagnostic solutions. JPRO works with engine, transmission and braking systems. The diagnostics software displays vehicle faults, and allows the user to record data for playback; view and chart engine parameters; print reports; and launch OEM software and troubleshooting guides. In addition to Class 7 and 8 vehicles, Noregon offers JPRO Commercial Fleet Products for medium-duty platforms, including Ford E-Series and F-Series trucks (model years 2004 and newer) and GM Class 2-6 trucks for model years 2002-2011. A broad spectrum of vehicle makes and models will be added throughout 2012.
Visit www.mitchell1.com/CommercialVehicleGroup/home.asp and www.noregon.com for more information.
Green Fleets, Fleet Maintenance