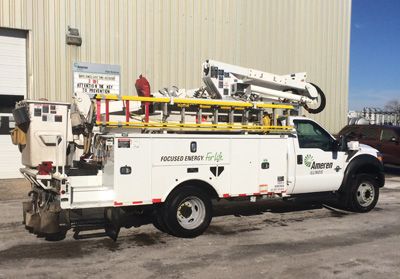
What to Expect in a Telematics Deployment
There’s a lot of hype around telematics – and for good reason.
When properly configured and maintained, telematics works like a sophisticated air traffic control system for your fleet. It uses GPS tracking and wireless connectivity to stream real-time vehicle location and performance data, giving you all the information you need – at a glance – to make smart decisions that reduce your fleet’s fuel costs and carbon footprint, improve vehicle utilization rates and promote safer driver behaviors.
But the qualifier here is the phrase “properly configured and maintained.” That’s because even when you’ve selected the right telematics system for your fleet, the installations and ongoing maintenance can get tricky, especially when you’re trying to track hundreds or thousands of fleet assets across multiple locations in a large service area.
At least that has been the experience for Ameren Illinois Company (AIC), a rate-regulated gas and electric utility headquartered in Collinsville, Ill., which completed its telematics hardware installations on about 2,300 vehicles and pieces of equipment in November 2014. The company currently has 3,300 total assets including trailers.
Overall Success
On one level, AIC has already received value from its telematics deployment, generating meaningful fuel cost savings the first full year (2015). This is largely attributed to engine idle reduction, according to Beth Daiber, CPA, supervisor of fleet administration for AIC.
Telematics has also helped AIC work with police to track down and recover a stolen asset, as GPS data showed the vehicle traveling through downtown St. Louis.
And AIC employees who are questioned about their driving or vehicle handling have found that telematics data can help set the record straight. “We can quickly pull the data and in many cases see that our drivers were operating safely,” Daiber said.
Data Quality Challenges
Yet, on a practical level, telematics is only as valuable as the quality of the data it generates. And sometimes that quality can be harder to achieve on a day-to-day basis than what you might expect, said Dan Remmert, manager of fleet services for AIC.
Take, for example, disruptions in wireless connectivity, where the vehicle’s GPS signal gets lost, leading to false reports.
“We’d pull idle reports on vehicles and started seeing odd data, such as a vehicle showing that it idled longer than the actual engine hours,” Remmert said. “You know it’s not correct, but it took us some time to figure out what was going on. In some cases, a vehicle would be in a garage and lose connectivity for several hours, but because of the programming of the software, when the signal returned, the data indicated that the vehicle had been idling when in reality it was parked and the ignition was shut off.”
How did AIC resolve the issue? “It was actually a third-party contractor performing on-site repairs on our vehicles who noticed that, when these units pulled into a garage, they lost GPS connectivity,” Daiber said. “Once we told our telematics provider what we were seeing with the garage issue, they were able to rectify it by making adjustments in the software logic.”
But sometimes disruptions in connectivity have nothing to do with the telematics hardware or software itself; if a backup asset sits too long, the vehicle’s battery will eventually die – and so will the GPS signal. At that point, the vehicle disappears from view, along with its data, impacting the accuracy of reports.
Getting unresponsive GPS units back online can be a challenge, especially for larger fleets, Daiber said. “The problem is, it’s never the same asset. You fix one, but then you’ve got three other ones that aren’t working. It’s a moving target.”
Real-World Advice
So, what are some lessons learned from AIC’s telematics deployment that you can apply to your own fleet? Remmert and Daiber offered these tips.
1. Network with peers.
“Network with other fleet managers in the utility industry to learn what has worked and what hasn’t,” Remmert said. “I think you really need to focus on getting advice within the utility industry because utility fleets have a unique set of needs and challenges that are different than those of, say, a delivery fleet.”
2. Plan for ongoing maintenance.
“Before you even start installations, have a plan as to how you’re going to maintain those units,” Daiber said. “That was something that I don’t think was fully on our radar before we got into this. We didn’t anticipate the amount of time it would take to maintain the hardware.”
3. Test data definitions during the pilot phase.
“When you’re doing a pilot [where the telematics provider allows you to test the system], really get down into the weeds about the data itself and test the reports so you’re actually getting what you think you’re getting,” Remmert said. “We really struggled with setting up our data definitions correctly upfront. I don’t blame that on the telematics provider. We had to understand what we wanted. What defines idle? What defines a backing event? You have to spend time working with your internal customers to determine what definitions they want set and then work with your telematics provider to help you get it done right.”
4. Get buy-in across the organization.
“Involving stakeholders throughout the company has been essential in the success of our telematics deployment,” Remmert said. “As an organization, we agreed that fleet would be responsible for managing the installs, maintenance and the reporting aspects of the system, but it’s really a full company initiative – not just fleet’s. We focused on getting all of senior leadership’s and other stakeholders’ buy-in before moving forward, which helped make the transition to GPS tracking go more smoothly.”
Daiber agreed. She said that when the fleet team set out to create an idle reduction policy to coincide with the telematics capabilities, they worked closely with AIC’s human resources group and equipment end users to craft a policy that would be practical and acceptable to all parties. “We went out into the field and received input from the end users, learning about their challenges, finding out why they idle their vehicles and uncovering ideas where we could reduce idle without negatively impacting driver productivity,” Daiber said. “We avoided creating an environment where the end users feel like they’re being watched and judged. That’s important to ensure that everyone is committed to continuous improvement.”
The Bottom Line
Despite some of the challenges his team has encountered with ensuring the quality of the data, Remmert said that, overall, telematics has transformed AIC’s fleet operations and is already generating actionable results. “At first you might feel like you’re beating your head against the wall, trying to manage all the complexities involved, but it’s worth it to get a final product that will help you manage your fleet performance more efficiently today and into the future,” he said.