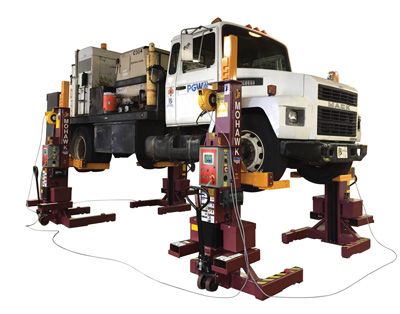
Choosing a Lift with Safety in Mind
When selecting a new maintenance bay lift that’s safe for your fleet operation, there’s more to consider than the assets that will be lifted on it. It’s also essential to account for what will be under and above the lift – and how the weight will be distributed.
All too often, industry experts say, well-meaning fleet professionals and maintenance technicians choose a lift simply based on the weight of the largest vehicle or piece of equipment it will hold. But there’s more to the equation, and getting it wrong can have disastrous results.
First, noted George Survant, senior director of fleet relations for NTEA – The Association for the Work Truck Industry (www.ntea.com), it’s important to remember that the base weight of an asset is one thing, but the weight of that asset when it’s on the lift, fully loaded, is another.
Here are seven additional considerations from Survant and Steve Perlstein, president of auto lift supplier Mohawk Lifts (www.mohawklifts.com), on choosing a lift with safety in mind.
- In terms of safety certification, Perlstein said “one and only one” matters: certification from the Automotive Lift Institute (www.autolift.org). Take note: There is an ALI requirement that all options and accessories used on a lift must be certified; if they’re not, the lift’s certification is void. That can make some options worthless. “People really should be checking and verifying not only that options are available, but the options are adequately rated,” Perlstein said.
- Proper sizing of a lift means knowing not just the overall weight of the largest vehicle it will hold, but also knowing the weight of that vehicle’s rear axle. “In the utility world, it’s only the back that matters,” Perlstein said.
- As trucks have gotten taller, Survant explained, “you need to make sure you have adequate headroom. If the lift could push the top of the truck through a low-hanging roof, and you have a new operator who is not familiar with that, they’ll give you a brand new skylight.”
- Ensure the lift is designed for the entire array of equipment it will hold, Survant said. Different assets may require different attachment points and configurations.
- If you’re thinking about potentially buying from a secondary market supplier, keep aftermarket support in mind. You don’t want to find yourself, years down the line, with a product you’ve bought from someone who is no longer in business – or one who has no relationship with the equipment manufacturer, Survant advised.
- Know the strength of the shop floor. Concrete can vary in thickness and strength, Survant said, “and that can be a problem if you put a new-generation lift in an older facility that perhaps wasn’t built for it.” Most new lifts have large feet to help distribute weight, “but it’s not impossible to find yourself in a set of circumstances the equipment wasn’t designed for,” he said.
- Training – both initial and ongoing – is critical. When was the last time your technicians were properly trained on safe use of a lift? Other types of training take place annually, Perlstein said, and it’s worth considering annual training for lifts, too. “God forbid something happen,” he said. “But if it does, at least you’ll have a paper trail to show that the technicians were trained. Our society has become so litigious, it’s what you now have to do.”
About the Author: Fiona Soltes is a longtime freelance writer based just outside Nashville, Tenn. Her regular clients represent a variety of sectors, including fleet, engineering, technology, logistics, business services, disaster preparedness and material handling. Prior to her freelance career, Soltes spent seven years as a staff writer for The Tennessean, a daily newspaper serving Nashville and the surrounding area.
*****
Safe Lift Operation Should Be ‘Intuitive’
What’s the main thing fleet professional George Survant would advise looking for in a lift?
Primarily, he said, that its proper use would be “intuitive.”
“What you find, in some of the older units, is that they have safeguards, tricks you need to know to make them safe,” he said. “But those tricks aren’t always obvious to technicians.”
He told the story of a mechanic who had a vehicle roll right off the back of a lift; certain supports were supposed to be upright as opposed to flat, Survant said, and the mechanic put up the supports in the front, but not the ones in the rear. “So as soon as he got it off the ground, it tilted backwards,” Survant said.
For those upfitting a garage with a new-generation lift, he explained, “one of the single most important characteristics is that the correct operation of the device is easy to identify. … It needs to be built in such a way that the lift won’t operate if the lift safety features aren’t engaged.”
Thankfully, Survant said, “the industry has taken a few giant steps forward” in lift design, especially when it comes to safety. “Back when I started, you had to fiddle with things all the time. You had to keep all your documentation in hand. And you had to worry about hydraulics. Units are nowhere near that complex today, and are so well-built and designed.”