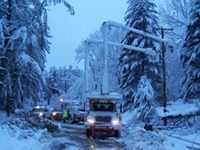
A92.2: The 2009 Standard
The Accredited Standard Committee (ASC) A92.2 Subcommittee for Vehicle Mounted Rotating and Elevating Aerial Devices of the American National Standards Institute (ANSI) has issued the long-awaited 2009 edition of the American National Standard for Vehicle Mounted Rotating and Elevated Aerial Devices.
Design and construction requirements of the original 1969 edition of A92.2 and its appendix were made a part of OSHA in 1970. Since then, the standard has been reissued in four editions in 1979, 1990 and 2001, and most recently in 2009. The 2009 Draft of the Standard was balloted twice by the committee and by ANSI rules was opened for public comment prior to final approval.
The newly revised A92.2 standard applies to the establishment of criteria for design, manufacture, testing, inspection, installation, maintenance, use, training and operation of vehicle-mounted aerial devices primarily used to position personnel installed on a chassis. The types of devices covered include extensible boom aerial devices, aerial ladders, articulating boom aerial devices, vertical towers or a combination of any of these.
An industry effort, the A92.2 subcommittee was a diverse group of between 30 and 36 individuals representing users and manufacturers. The subcommittee worked on the standard from 2001 until its eventual approval in July 2009.
For much of that time, the subcommittee was led by Gary McAlexander, president of Intercontinental Equipment Company. McAlexander, who joined the A92 revision effort in 1981, was chairman of the A92.2 subcommittee from 2001 until the 2009 revision was approved.
“The ongoing revision process for a standard like A92.2 is important because it ensures the safety of the utility crews that use aerial devices on a daily basis,” McAlexander said. “By reflecting the changes that have occurred in aerial design, work practices and regulations, we can help reduce incidents in real world operations.
“Communication is important in all endeavors,” McAlexander continued, “and in this case the exchange of information between manufacturers and users was especially valuable. This industry effort involving suppliers and utilities has helped ensure that a workable, effective and comprehensive standard is in effect.”
Joshua Chard, Ph.D., director – product & corporate safety at Altec Inc. now serves as chairman of the A92.2 subcommittee that completed its work on the newly revised standard. In June 2010, he covered the standard and its most recent changes at the 57th annual Electric Utility Fleet Managers Conference in Williamsburg, Virginia.
“The 2009 version of the standard contains many evolutionary changes,” Chard explained. “These changes contain the best language that could be agreed upon by the ANSI/ASC Subcommittee and Main Committee. In all cases they are meant to further the standard in its goal, “to prevent accidents associated with the use of Vehicle Mounted Elevating and Rotating Aerial Devices by establishing requirements for design manufacture, installation, maintenance, performance, use and training.”
Key Elements
The following represent some of the key elements of the newly revised ANSI A92.2 standard issued in 2009 that Chard covered in his presentation.
Although the requirements for general training carry over from the 2001 standard, a fourth bullet was added to the requirements for familiarization.
8.12.3 Familiarization – When an operator is directed to operate an aerial device they are not familiar with, the operator, prior to operating, shall be instructed regarding the following items:
1. The location of the manuals.
2. The purpose and function of all controls.
3. Safety devices and operating characteristics specific to the aerial device.
4. Under the direction of a qualified person, the trainee shall operate the aerial device for a sufficient period of time to demonstrate proficiency in the actual operation of the aerial device.
Additionally, the standard discusses the different types of qualified persons who typically operate aerial devices.
APPENDIX F – PRECAUTIONS FOR USE OF AERIAL DEVICES ON OR NEAR ENGERGIZED APPARATUS
Unqualified Person: A person who does not have approval to approach energized lines and apparatus and has received no significant training regarding the electrical hazards involved in the placing of an aerial device, platform occupants and their tools closer to energized lines and facilities than the distances listed.
Qualified Person: A person who has received training, understands and is conversant in the electrical hazards involved in the placing of an aerial device, platform occupants and their tools closer to energized lines and facilities than the distances listed, and has approval to perform the work.
Training of qualified person(s) is the responsibility of the employer or his designated contractor(s) and can be classroom, hands-on or a combination, as deemed appropriate by the employer for the degree of risk involved.
An unqualified person, as an operator, shall not approach energized conductors or facilities that will place the insulating or non-insulating aerial device, the operator and other platform occupants, and their tools, closer to such facilities that the distances shown.
A qualified communications person, as an operator, shall not approach energized conductors or facilities that will place the insulating or non-insulating aerial device, the operator and other platform occupants, and their tools, closer to such facilities than the distances set forth in Part 29 CFR 1910.268 and the National Electrical Safety Code.
A qualified line clearance tree trimmer, as an operator, shall not approach energized conductors or facilities that will place the insulating or non-insulating aerial device, the operator and other occupants, and their tools, closer to such facilities than the distances set forth in Parts 29 CFR 1910.268, 1910.269 or ANSI/ISA Z133.1.
A qualified lineman, as an operator, shall not approach energized conductors or facilities that will place the insulating or non-insulating aerial device, the operator and other platform occupants, and their tools, closer to such facilities than the distances set forth in Part 29 CFR 1910.269 and the National Electrical Safety Code. Higher levels of qualifications are required for electrical linemen to physically contact energized conductors and facilities from Category A, B and C aerial devices.
DEFINITIONS
The definitions section was expanded during the revision process. Of note was a clarification as to the role of the chassis insulating system:
Chassis Insulating System – An insulating system of dielectric components installed between the chassis and the upper insulating boom.
5.2.5 The chassis insulating system may provide some protection for ground personnel should the portion of the aerial device between the upper insulating boom and the chassis insulating system inadvertently contact an energized conductor or apparatus such as a secondary circuit on a distribution system. When provided, the chassis insulating system does not have a voltage rating. Aerial devices with a chassis insulating system shall have means provided to bypass the chassis insulating system during electrical test, or bare-hand use.
Note: Insulating devices when used for bare-hand work (Category A) require shunting of an existing chassis insulating system.
Insulated Insulating Aerial Device – An aerial device with dielectric components designed and tested to meet the specific electrical insulating rating consistent with the manufacturer’s identification plate.
A significant change found in the design of insulated units is a requirement that lower controls be readily accessible in all boom positions and be installed such that an operator is not placed in the electrical path between the aerial device and the ground.
4.3.3 Lower Controls – Lower controls shall be readily accessible in all boom positions and shall provide a means to override the boom positioning upper controls provided the upper control system is intact.
The override mode shall maintain its function while unattended. The lower controls of insulating aerial devices shall be designed in such a manner that an operator is not placed in the electrical path between the aerial device and the ground
Two new requirements for operator aids are a slope indicator and an outrigger interlock device.
4.5.4 Slope Indicator – An indicator(s) shall be provided that is visible to the operator during setup to show whether the aerial device is positioned within limits permitted by the manufacturer. The allowable limits shall be shown on the unit and in the manual. For units designed for mobile operation such an indicator(s) shall be supplied in the cab.
4.5.5 Outrigger Interlock Device – When an aerial device is equipped with outriggers, and their use is required to pass the stability tests of this standard, an interlock device shall be provided that prevents the boom from being operated from the stowed position until the outriggers have been deployed.
Deployment may be sensed when the outriggers meet resistance or by receipt of an indicative response that the outrigger deployment is beyond a predetermined position. The lifting of an outrigger during operation shall not disable boom functions. An interlock override switch may be provided; however, the override mode of operation shall disable automatically.
Note: The operation of outrigger interlocking devices does not assure aerial device stability. It serves only to remind the operator that the outriggers have or have not been deployed. See Section 10.10 (3). Changes were also made to the fall protection anchorage section.
4.9.4 Anchorage(s) for Personal Fall Protection
4.9.4.1 The manufacturer shall provide anchorage(s) on the boom, platform or platform mounting.
4.9.4.2 The location of the anchorage(s) shall be identified and the number of anchorages shall equal or exceed the number of permissible occupants. More than one occupant may attach to a single anchorage if the anchorage is rated and identified as being for more than one person.
4.9.4.3 Strength requirement. Anchorages shall be capable of withstanding a static force of 3,600 lbs. (16,000N) for each person allowed by the manufacturer on the attachment without reaching ultimate strength. The strength requirement shall apply only to the anchorage(s) and their attachments to the boom, platform or platform mounting.
Note: This does not imply that the aerial device is meant to meet or comply with this load requirement.
4.9.4.4 Connector requirement. Anchorage shall be compatible with a lanyard connector complying with ANSI/ASSE Z359.1-2007.
4.9.4.5 Surface. Anchorage(s) surfaces shall be free from sharp edges.
4.9.4.6 Pinch restriction. A lanyard connector shall not pinch between components having relative movement with the anchorage(s).
Note: See Sections 8.12.1, 9.3.1, 10.12.1 and 11.4.1 for more information pertaining to proper use of personal fall protection equipment.
The revision of the standard also made changes in the electrical sections. It clarifies the categories of insulated units with special attention given to the type of protection offered to the worker by the unit versus personal protective equipment.
5.1 Electrical Specifications – An aerial device with an insulated upper boom is commonly used to provide an additional layer of secondary protection from a path to ground through the boom and vehicle. This secondary protection is valuable; however, it cannot replace the worker’s primary protective equipment.
ANSI A92.2 CATEGORIES
Category A – Aerial devices which are designed and manufactured for work in which the boom is considered primary insulation (bare-hand work) shall have all conductive components at the platform end bonded together to accomplish equipotential of all such components. These aerial devices shall be equipped with a lower test electrode system. When these aerial devices are qualified for work above 138 kV, they shall be equipped with a gradient control device and conductive shield(s) over the lower test electrode system. For those aerial devices with ratings 138 kV and below, conductive shield(s) over the lower test electrode system are required. The necessity of a gradient control device is to be determined by the Qualification test.
Category B – Aerial devices which are equipped with a lower test electrode system, but are designed and manufactured for work in which the boom is not considered as primary insulation, but secondary, such as that using insulating (rubber) gloves. Category B aerial devices can be rated higher than 46 kV in order to facilitate changing them to Category A aerial devices for “bare-hand work.”
The manufacturer is reminded to consider in the design that “bare-hand work” requires the use of Category A aerial devices. Using Category B aerial devices on voltage levels above 46 kV requires the use of live line tools with appropriate dielectric ratings. These tools are to be depended upon for primary protection, just as in all cases where the boom is used as secondary protection (Categories B and C).
Category C – Aerial devices which are not equipped with a lower test electrode system and are designed and manufactured for work in which the boom is not considered as primary insulation, but secondary, such as that using insulating (rubber) gloves. These aerial devices are designed for voltages of 46 kV and below.
5.2.1 Insulating Systems – The insulating portions of the aerial device shall be identified in the manual and on the aerial device. All components crossing the insulating portions of the aerial device shall have electrical insulating values consistent with the design voltage rating of the boom, and when provided, of the chassis insulating system. The insulating system shall maintain the electrical insulating values in all working boom positions as defined by the manufacturer.
The above information is important to understand in light of the presence of metal components above the unit’s insulating sections.
CONDUCTIVE BOOM TIP
Contact of any component at the boom-tip with an energized conductor can energize all components at the boom-tip, including the control handle.
This concept is important when maintaining minimum approach distances to boom tip components.
1910.269 (l)(2) Minimum Approach Distances – The employer shall ensure that no employee approaches or takes any conductive object closer to exposed energized parts than set forth in Table R-6 through Table R-10, unless:
(i) The employee is insulated from the energized part (insulating gloves or insulating gloves and sleeves worn in accordance with paragraph (l)(3) of this section are considered insulation of the employee only with regard to the energized part upon which work is being performed).
(ii) The energized part is insulated from the employee and from any other conductive object at a different potential.
(iii) The employee is insulated from any other exposed conductive object, as during live-line bare-hand work.
Note: Paragraphs (u)(5)(i) and (v)(5)(i) of this section contain requirements for the guarding and isolation of live parts. Parts of electric circuits that meet these two provisions are not considered as “exposed” unless a guard is removed or an employee enters the space intended to provide isolation from the live parts.
The revision of A92.2 for 2009 addresses this issue with allowances for control systems that incorporate High Electrical Resistance Components.
5.2.6 Upper Controls – The upper control conductive components are bonded together on Category A machines, but such bonding is optional on Category B and Category C machines. Categories B and C machines may incorporate control systems with high electrical resistance components. Machines that incorporate components for their electrical resistance shall receive an initial confirmation test and be subjected to the requirements for periodic inspections (See Sections 5.4.2.6, 5.4.3.6).
Controls that employ high electrical resistance components do not have a voltage rating and are not part of the insulating system that enables an aerial device to have an insulating rating. Whatever upper control arrangement is provided shall be identified. Specific warnings and advice shall be provided to the operator(s) that the upper controls do not provide protection in the event of electrical contact and are not a substitute for Minimum Approach Distances, cover-ups, rubber gloves and other personal protective equipment.
5.4.2.6 Confirmation test of upper control components with high electrical resistance. Upper controls that incorporate components for their electrical resistance shall be tested to assure resistance by testing them at 40 kV 60 Hz r.m.s. for 3 minutes with a maximum current level of 400 microamperes.
5.4.3.6 (Periodic) Confirmation Test of Upper Control Components with High Electrical Resistance. Upper controls that incorporate components for their electrical resistance should be tested to assure resistance by testing them at either 40 kV AC or 56 kV DC for 3 minutes with a maximum current level of 400 microamperes for the AC test and 56 microamperes for the DC test.
Covers and High Electrical Resistance upper controls offer new layers of protection for users of insulated aerial devices. This protection is valuable; however, it cannot replace the worker’s primary protective equipment.
Also dealing with this issue were changes to the requirements for manuals:
6.4 Manuals – The manufacturer shall provide a separate operators manual and a separate parts/ maintenance manual for each aerial device. Two sets of manuals shall accompany each device. The manuals shall contain:
(8) Facsimiles of all safety and operating decals and their location.
6.5.4 Instructional Markings. Markings shall be determined by the manufacturer or the manufacturer and user jointly to indicate hazards inherent in the operation of an aerial device. Instructional markings shall be provided for:
(9) Notice that fiberglass or plastic covers are not insulating.
(10) Notice that the aerial device shall not be operated with missing covers or guards, except as required for maintenance to the aerial device.
RESPONSIBILITIES OF DEALERS AND INSTALLERS
7.8 Training: The dealer or installer shall offer training or training materials that aid owners, users, operators, lessors and lessees in the operation, inspection, testing and maintenance of the aerial device. This training shall be offered initially and subsequently on request.
7.9 Maintenance Training: Dealer maintenance personnel shall be trained in inspection, testing and maintenance of the aerial device in accordance with the manufacturer’s recommendations.
7.8.1 Dealer or Installer as User: Whenever a dealer or installer directs personnel to operate an aerial device (inspecting, sales demonstrations or any form of use), the dealer or installer shall assume the responsibilities of users as specified in Section 9 of this standard. All personnel authorized to operate the aerial device shall have been trained in a program that meets the requirements of this standard.
Section 8 Responsibilities of Owners was reorganized and new items were added in the inspection and test requirements:
8.2.3 Frequent Inspection and Test – The following inspections and tests shall be performed by the operator immediately prior to first use at the beginning of each shift:
1. Conduct walk-around visual inspection looking for damaged components, cracks or corrosion, excessive wear and any loose, deformed or missing bolts, pins, fasteners, locking devices and covers.
2. Check all controls and associated mechanisms for proper operation to include, but not limited to, the following:
a. Proper operation of interlocks.
b. Controls return to neutral when released and not sticking.
c. Control functions and operation clearly marked.
3. Check visual and audible safety devices for proper operation.
4. Visually inspect fiberglass and insulating components for visible damage and contamination.
5. Check for missing or illegible operational and instructional markings.
6. Check hydraulic and pneumatic systems for observable deterioration and excessive leakage.
7. Check electrical systems related to the aerial device for malfunction, signs of excessive deterioration, dirt and moisture accumulation.
8. Perform functional test to include, but not limited to, the following:
a. Set up aerial device for operation, including outriggers.
b. Cycle each aerial device boom function through its complete range of motion from the lower controls, except where operation through the complete range of motion would create a hazard.
c. Check functionality of emergency controls.
Any suspected items shall be carefully examined or tested and a determination made by a qualified person as to whether they constitute a safety hazard. All unsafe items shall be replaced or repaired before use.
8.2.4 Periodic Inspection or Test
(13) Condition and tightness of bolts and other fasteners in accordance with the manufacturer’s recommendation.
(17) If the aerial device has upper controls equipped with high electrical resistance components and the manufacturer so indicates, they should be electrically tested per 5.4.3.6.
Any suspected items shall be carefully examined or tested and a determination made by a qualified person as to whether they constitute a safety hazard. All unsafe items shall be replaced or repaired before use.
8.2.5 Post Event Inspection or Test – After any reported event during which structural members of an aerial device or mobile unit are suspected of being subjected to loading or stresses in excess of design stress, such as after an accident involving overturning of the mobile unit or application of unintended external mechanical or electrical forces to the aerial device, the aerial device shall be removed from service and subjected to the applicable periodic inspection requirements in 8.2.4. In addition to the periodic inspection, supplemental non-destructive examination procedures or other tests to assist in detecting possible structural damage to the aerial device may be required. All damaged items shall be replaced or repaired before the unit is returned to service.
Also in Section 8 are some requirements for proper welding, use of aerial devices for intended applications, ownership notification and a prohibition on certain alterations.
8.4.2 Welding – Welding repairs of components or welds, designated as critical in the manufacturer’s manual shall be made in accordance with the manufacturer’s recommendations and shall meet the Structural Welding Code AWS D1.1-2006 and AWS D1.2-2003. Should the original manufacturer no longer exist, an equivalent entity may determine the required procedure.
8.5.1 Alterations – Altering or disabling the function of safety devices, guards or interlocks, if so equipped, shall be prohibited.
8.7 Transfer of Ownership – When a change in ownership of an aerial device occurs, it shall be the responsibility of the seller to provide the manufacturer’s manual(s) for that aerial device to the purchaser. It is the responsibility of the purchaser to notify the manufacturer of the unit model and serial number and the name and address of the new owner within 60 days. If the owner uses other entities as agents, e.g., brokers, for the sale or the arrangement of a sale of an aerial device(s) his responsibilities under this section continue.
9.4 Application – The employer and authorized operator(s) shall ensure that the aerial device is used only for intended applications as defined in the operating manual and that all recognized safety practices are observed.
Note: The user is directed to Appendix C for guidance as to appropriate applications.
9.5 Electrical Hazard – All applicable safety-related work practices intended to protect from electrical hazards shall be defined and explained to the operator by a qualified person. The operator shall maintain the appropriate Minimum Approach Distance (MAD) from energized conductors and apparatus, commensurate with the operator’s qualifications. See Appendix F for the information on the Minimum Approach Distances and other precautions.
The operators section was also reorganized to match the inspection requirements in Section 8.
RESPONSIBILITIES OF OPERATORS
10.7 Alterations – Altering or disabling the function of safety devices, guards or interlocks, if so equipped, is prohibited.
10.8 Observations – Observations during operation for any defects shall be conducted on an ongoing basis.
10.8.1 Pre-start Inspection
1. Conduct walk-around visual inspection, looking for damaged components, cracks or corrosion, excessive wear and any loose, deformed or missing bolts, pins, fasteners, locking devices or covers.
2. Check all controls and associated mechanisms for proper operation to include, but not limited to, the following:
a. Proper operation of interlocks.
b. Controls return to neutral when released and not sticking.
c. Control functions and operation clearly marked.
3. Check visual and audible safety devices for proper operation.
4. Visually inspect fiberglass and insulating components for visible damage and contamination.
5. Check for missing or illegible operational and instructional markings.
6. Check hydraulic and pneumatic systems for observable deterioration and excessive leakage.
7. Check electrical systems related to the aerial device for malfunction, signs of excessive deterioration dirt and moisture accumulation.
8. Perform functional test to include, but not limited, to the following:
a. Set up aerial device for operation, including outriggers.
b. Cycle each aerial device boom function through its complete range of motion from the lower controls, except where operation through the complete range of motion would create a hazard.
c. Check functionality of emergency controls.
Any suspected items shall be carefully examined or tested and a determination made by a qualified person as to whether they constitute a safety hazard. All unsafe items shall be replaced or repaired before use.
10.9 Worksite – Before the aerial device is used, the worksite shall be surveyed for hazards such as:
1. Insufficient supporting surfaces such as soft ground or tamped earth fills.
2. Ditches.
3. Excessive slopes, drop-offs, curbs and floor obstructions.
4. Debris.
5. Overhead obstructions and electrical conductors.
6. Weather conditions.
7. Presence of unauthorized persons.
8. Road or worksite traffic.
9. Subsurface chambers such as underground utility components or septic systems.
The standard includes a new appendix, which discusses concepts important for work around energized conductors.
HANDLING ENERGIZED APPARATUS (APPENDIX F)
When the boom tip jib and/or winch of a category B or C aerial device is used for handling energized conductors and apparatus, the energized conductors and apparatus shall be insulated from the boom tip with electrical protection devices that are rated, tested and maintained for the appropriate rated line voltage.
Boom tip jibs used in material handling on aerial devices shall be considered non-insulating unless the jib has been rated, tested and maintained for the appropriate line voltage.
Safety rules and work practices may vary significantly for different users, but one universal rule that applies is when jibs are used as a live-line tool with category B and C aerial devices, platform occupant(s) must use protective equipment such as gloves and cover-ups.
If the winch line is used to lift energized apparatus, the energized apparatus shall be insulated from the jib tip with electrical protection devices that are rated, tested and maintained for the appropriate line voltage.
The winch line shall not be considered as insulating. For multi-phase lifting with conductor holders and a cross-arm, phase to phase protection shall be accomplished with a cross-arm that is rated, tested and maintained for the appropriate line voltage.
Insulating Liners and Insulating Baskets – A dielectrically tested insulating liner or insulating basket is intended to prevent electrical current flow through the lower extremities of the basket occupant. This is one element in a system approach that includes both work practices and materials designed to avoid electrical contact. Such a liner or basket shall not be considered primary insulation.
Minimum approach distances must be maintained by the electrical worker to assure clearances between objects at different electrical potential when performing live-line work. It applies to the worker’s reach including any non-insulating object above the insulated section of the aerial device. The Minimum Approach Distances may be obtained from sources such as, but not limited to:
ANSI C-2 National Electrical Safety Code
ANSI C-1 National Electrical Code
CFR 29 1926.950
CFR 29 1910.269
Work practices
(j) Live-line tools.
(1) Design of tools. Live-line tool rods, tubes and poles shall be designed and constructed to withstand the following minimum tests: (i) 100,000 volts per foot (3281 volts per centimeter) of length for 5 minutes if the tool is made of fiberglass-reinforced plastic (FRP).
(2) Condition of tools.
(i) Each live-line tool shall be wiped clean and visually inspected for defects before use each day.
(ii) If any defect or contamination that could adversely affect the insulating qualities or mechanical integrity of the live-line tool is present after wiping, the tool shall be removed from service and examined and tested according to paragraph (j)(2)(iii) of this section before being returned to service.
(iii) Live-line tools used for primary employee protection shall be removed from service every two years and whenever required under paragraph (j)(2)(ii) of this section for examination, cleaning, repair and testing.
Editor’s Note: The annual Electric Utility Fleet Managers Conference (EUFMC) hosts representatives of more than 50 companies in the U.S. and Canada, including investor-owned electric utilities, electric cooperatives and electrical contractors, and more than 270 representatives from more than 95 manufacturers and service providers. The conference includes an Equipment Demonstration and Display, which in 2010 was the site of more than 60 exhibits. EUFMC will be held June 19-22, 2011 at the Williamsburg Lodge and Conference Center in Williamsburg, Va. For more information, visit www.eufmc.com.