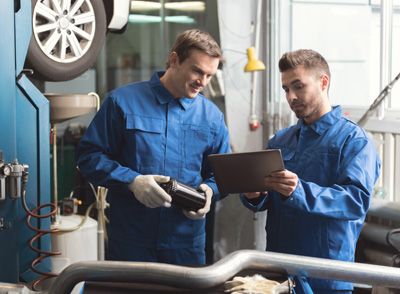
Strategies for Addressing the Looming Technician Shortage
With more baby boomers heading into retirement, industries that have benefited from these individuals’ decades of experience and expertise — including the utility fleet sector — are now left to hire and retain new talent.
That won’t be easy, according to Jennifer Maher, CEO and executive director of TechForce Foundation (www.techforcefoundation.org), whose mission is to champion students to and through their education and into careers as professional technicians. “There has been a critical shortage of qualified technicians for at least 20 years, so as the rest of the baby boomers retire within the next 10 years, things can only worsen. A report that we published late last year indicated that for this year alone, the vehicle industry – auto, diesel and collision – needs more than 137,000 new-entrant technicians.”
But it’s not just the retirements that will make matters worse, Maher said. “There simply are not enough young people seeking a technician career by any means – formal or informal education and training – to fill the void. Our school systems in this country have either reduced or eliminated vocational training in favor of a four-year degree. In effect, they have abandoned working with your hands as a viable career path, which is absurd not only because of the tech shortage, but also because a tech career offers a solid, middle-class lifestyle.”
So, what can utility fleets do to address this problem – and what should they opt not to do?
“The worst thing utility fleet managers can do is take a wait-and-see attitude. When you don’t have enough qualified techs to service the fleet, no matter which one, there is going to be a loss in productivity and efficiency,” Maher said. “The entire industry – associations, manufacturers, service facilities, et cetera – has to come together to solve the problem. For the sake of the industry, even competitors will have to check their self-interests at the door.”
A Tough Task
It’s no surprise that fleets seek to hire experienced candidates to replace those employees who have retired or left the company for other reasons. But some losses make more of an impact than others, and replacing those workers typically isn’t easy.
For example, John Adkisson, transportation manager for PPL Electric Utilities, said that it’s a major loss when employees who can work on hydraulic aerial devices or specialized equipment – and who can train others to do the same – leave the company. “We usually make sure techs come from technical schools or have a body of knowledge from prior job experience, but the hydraulic training is coming from in-house,” he said.
To address this issue, PPL hired a former hydraulic mechanic in October 2017 to serve as an in-house instructor and share his knowledge with others. “Eighty percent of his time is spent training; the rest is on actual maintenance. When there is an opportunity for the specialized hydraulic work, the less-seasoned techs use that time for on-the-job training,” Adkisson said.
Proactive Approach
Nebraska Public Power District (NPPD) has taken a proactive approach to attracting prospective employees by working with several area technical colleges over the past four years to increase the pool of qualified candidates for its fleet. Initially, however, there wasn’t much interest from the students.
“A lot of these students going into vocational tech schools already have a preconceived notion of what they want to do when they leave,” explained Matt Gilliland, director of transportation and facilities for NPPD. “They go into it to work at Caterpillar or end up at Deere. When you hear ‘utility,’ it’s easy to automatically jump to the conclusion of line-type work rather than the fleet service.”
To spark greater interest, NPPD decided to bring fleet equipment into the schools and hold utility demonstration events. During these events, staff from the utility go into classrooms and provide 10- to 15-minute presentations about how the equipment operates, what they work on and some of the challenges they face.
“That builds excitement, and then we have the candidate pool,” Gilliland said.
NPPD employees also serve on the advisory boards of these colleges, which has allowed them to provide input on some of the curriculum and order of class schedules. That also presented the opportunity for an internship program. “Typically it starts with some shadowing, they get some familiarity,” Gilliland said. “We have the opportunity then to have a second person on board for jobs that require two people. Eventually, as they mature in the internship, they typically work on their own.”
NPPD offers one to two paid internships per year, ranging from 20 to 40 hours per week during its regular Monday to Friday, 7 a.m. to 4 p.m. schedule. Hours are flexible to accommodate students’ class schedules. Gilliland said the program has worked out well, with students moving on to take positions with other utilities as well as vendors that service utilities.
For other fleets interested in implementing a similar program, Gilliland suggested contacting local tech schools to find out about their current internship programs, how they work, and whether they’re done on a semester or quarterly basis.
“Then just have an open dialogue about what you and the company want to get from that internship and what the school can provide, then jointly create that opportunity,” Gilliland said.
About the Author: Grace Suizo has been covering the automotive fleet industry since 2007. She spent six years as an editor for five fleet publications and has written more than 100 articles geared toward both commercial and public sector fleets.
*****
Starting at the Grassroots Level
Whether a fleet will be able to adequately fill the roles of seasoned employees when they leave the company will depend on several factors. It’s helpful to have a plan in place and take advantage of available resources.
“If we’re going to solve the qualified technician shortage problem, we need to work at the grassroots level, offering tangible and relevant experiences to adolescents as they start to think about their careers,” said Jennifer Maher, CEO and executive director of TechForce Foundation.
Local community colleges and training schools are good places to begin recruiting candidates, in addition to hosting on-site job fairs where students and parents can gain a better understanding of what fleet businesses do and how they do it.
Maher also noted the Technology & Maintenance Council’s annual National Technician Skills Competition – also known as TMCSuperTech – which attracts contestants from all segments of the industry, many of whom have won state, regional and corporate skills championships.
“If a fleet manager wants to hire the techs with the most potential, these competitions provide ready-made opportunities to start a conversation with them,” Maher said.
TechForce recently unveiled its revamped website (www.techforcefoundation.org), designed, built and managed by Autoshop Solutions. The new site includes the FutureTech Resource Hub, a one-stop-shop portal through which future technicians can find after-school programs, clubs, events, technical schools, scholarships and training that help develop their skills and pathway to the technician profession. Additionally, the site includes the new Industry Hub, through which industry recruiters, managers, working technicians and educators can find helpful resources to support and connect with future technicians.